www.modernitovarna.com
03
'18
Written on Modified on
Realita současné výrobní ekonomiky
Úsilím všech výrobců je zajištění produkce určitého počtu obrobků v potřebné kvalitě, v daném čase a za rozumnou cenu. Opakované dosahování těchto cílů spočívá v řízení mnoha faktorů, mezi které patří řezné parametry, náklady na nástroje a čas vynaložený na jejich výměnu, využití obráběcího stroje, manipulace s obrobky, jakož i náklady na materiál a mzdy zaměstnanců.
Ekonomika výroby vyžaduje cílené vyvážení procesních faktorů tak, aby bylo dosaženo požadovaných výsledků. Za více než dvě století historie obrábění se množství faktorů ekonomiky výroby zmnohonásobilo. Výroba se nejprve vyvinula od ručního zhotovování individuálních výrobků po hromadnou výrobu standardizovaných dílů s použitím obráběcích strojů. Zdokonalování výrobních postupů pak přineslo druhou generaci hromadné výroby s výrobními linkami, které jsou schopny produkovat stále větší objemy identických dílů – výroba s velkým objemem a nízkou variabilitu výrobků (HVLM). CNC stroje a roboty přinesly třetí generaci efektivity hromadné výroby. V poslední době se hovoří o čtvrté generaci hromadné výroby označované jako Průmysl 4.0, která umožňuje nákladově efektivní vysoce různorodou výrobu malých objemů (HMLV).
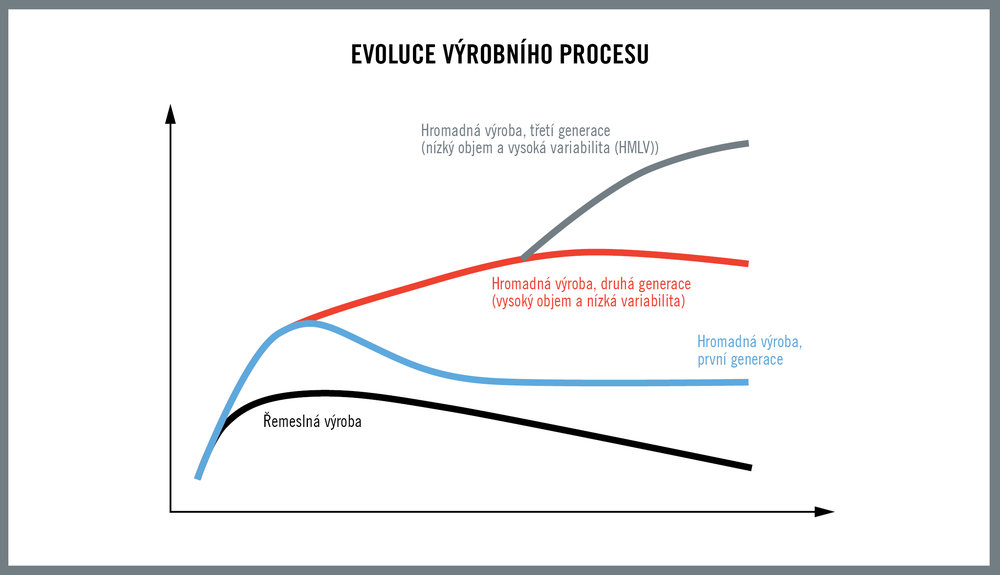
HQ_POS_vyvoj_procesu_vyroby.jpg
Pro efektivní přechod od výroby HVLM na HMLV je důležité, aby si výrobci uvědomili změny a skutečnosti výrobní ekonomiky a využili výhody informací a technologií analýzy výrobního procesu pro odhalení neefektivních postupů a zjištění příležitostí ke zlepšení. Klíčový prvek transformace zahrnuje opuštění přehnaně zjednodušených názorů a postupů a odhalení skrytých nákladů, které mohou podkopávat snahy o maximalizaci produktivity.
Velký objem, nízká variabilita, jednoduchá ekonomika?
Standardizované procesy obrábění byly vyvinuty v 19. století k urychlení produkce identických výrobků se zaměnitelnými součástmi. Automobilová výroba tento přístup HVLM zdokonalila na maximální míru, přičemž zavedla dopravníkové linky a další postupy pro výrobu stovek tisíců nebo dokonce milionů stejných produktů stále dokola i po několik let.
Dlouhodobá povaha výroby HVLM umožňuje výrobcům jemně doladit vícero výrobních faktorů s ohledem na dosažení maximálního výkonu a opakovatelnosti a minimalizaci nákladů. Variabilitu dále snižují pomocné technologie zahrnující systémy pro výměnu nástrojů a palet, a také roboty. Předpokladem je, že výrobní proces poběží dokonale a poskytne 100procentní výnos s předvídatelnými náklady bez neplánovaných prostojů, zmetků, potřeby přepracování a sekundárních úkonů, jako např. odstraňování otřepů.
Dále se předpokládá, že náklady na nástroje činí obvykle zhruba tři procenta celkových výrobních nákladů. Tříprocentní hodnota představuje snadno použitelné srovnávací měřítko, které ale zřídkakdy platí. Velký vliv mají například vlastnosti materiálu obrobku – přechod z ocele na titan při obrábění může znamenat až pětinásobné zvýšení spotřeby nástrojů. Z tříprocentního podílu se stane 15 procent, zatímco ostatní parametry zůstanou stejné.
Výhradní zaměření na dobu záběru nástroje má za následek zanedbávání ostatních faktorů, jako jsou například prostoje při výměně nástrojů. Tento přístup tak bohužel zakrývá pravou realitu. Výrobci by měli pochopit, že doba obrábění, doba přípravy, čas potřebný na výměnu nástrojů, zakládání a vyjímání obrobků a další faktory se vzájemně ovlivňují a narušují.
Zjednodušený příklad neočekávaných procesních faktorů představuje výroba dílu, který vyžaduje dvě minuty na obrobení a další dvě minuty na vložení a vyjmutí obrobku. Výměna břitových destiček vyžaduje minutu času, přičemž životnost nástroje je pět obrobků, takže čas na výměnu destičky je 0,2 minuty na díl. Protože zpracování každého dílu trvá 4,2 minuty, za hodinu lze vyrobit 14 obrobků. Cena nástroje je 15 eur a podle životnosti nástroje (pět obrobků) vychází, že na 14 obrobků je potřeba 2,8 nástroje (42 eur). Náklady na stroj jsou 50 eur/hod. Celkové výrobní náklady na zpracování 14 obrobků za jednu hodinu tedy činí 92 eur.
Následně se výroba, ve snaze o maximalizaci výkonu a produktivity, rozhodne zvýšit řeznou rychlost o 10 procent. Tím se zkrátí doba obrábění o 10 procent (na 1,8 minuty), ale také dojde ke snížení životnosti nástroje zhruba na polovinu, což znamená, že jedna řezná hrana obrobí pouze dva a půl obrobku do chvíle, než bude potřeba provést její výměnu. Čas potřebný na výměnu nástroje je stále jedna minuta a doba pro upnutí a uvolnění obrobku dvě minuty. Čas na zpracování jednoho dílce zůstává 4,2 minuty (1,8 minuty obrobení, 2 minuty manipulace s obrobkem a 0,4 minuty výměna nástroje), a vyrobí se stejný počet - 14 obrobků za hodinu. Náklady na stroj a nástroje jsou stejné, ale nyní je pro hodinový výrobní cyklus potřeba 5,6 nástroje (náklady na nástroje 84 eur). Navzdory snaze o zvýšení rychlosti výstupu je výrobní čas pro 14 obrobků stejný a náklady se přitom zvedly z 92 eur na 134 eur.
V takovém případě zvyšování řezné rychlosti vyšší produktivitu nepřinese. Změna doby obrábění ovlivňuje jiné faktory obráběcího procesu, v tomto případě životnost nástroje a čas potřebný pro jeho výměnu. Podle toho musí výrobci pečlivě zvážit všechny důsledky změn ve výrobním procesu.
Další skryté náklady představuje provádění určitých kroků v procesu obrábění. V mnoha provozech je učebnicovým příkladem skrytých nákladů například čas strávený výměnou břitových destiček. Čas určený na výměnu břitové destičky může být jedna minuta. Pokud se však změří skutečný čas ve výrobě, může jít o dvě, tři nebo deset minut, což je rozdíl 60 až 600 vteřin.

HQ_ILL_Vyrobni_naklady_a_obrabeni_jako_funkce_zvysovani_prostoju.jpg
Obrázek 2
Vysoká variabilita, nízký objem, komplexní rozvažování
V poslední době jsou výrobci nuceni celosvětovou konkurencí vyrábět pro uspokojení potřeb menších podskupin uživatelů různé verze svých výrobků. Pokročilé výpočetní technologie umožňují rychlé změny v konstrukci dílu i obráběcích programů, a také snadné sledování variability výrobku a skladových zásob. Výsledkem je přesun k výrobním scénářům s nízkoobjemovou výrobou a vysokou variabilitou (HMLV). V současnosti je tento přístup dostatečně rozvinutý, aby umožnil efektivní výrobu v malých dávkách, například do deseti kusů, nebo se dokonce může jednat o zakázkovou výrobu jednotkových počtů.
Širší časový horizont výroby HVLM umožňuje promyšlené plánování a jemné doladění procesních faktorů. Plánování ve scénářích HMLV je odlišné. Počítačové technologie přípravy výroby a řízení skladových zásob podporují rychlé změny typu výrobku a výstupu, což ale do procesu výroby HMLV přináší nutnost komplexního a reaktivního plánování. Po objednávce deseti dílů může následovat požadavek na série dvou nebo pěti nebo dokonce jednotlivých položek různých dílů. Obráběné materiály se mohou měnit z ocele na hliník a titan a geometrie dílů z jednoduché na složitou. Není dostatek času na určení životnosti nástroje prostřednictvím zkušebních sérií.
V rámci řízení životnosti nástroje při výrobě typu HMLV výroba obvykle provede konzervativní odhad plánované životnosti nástroje a z důvodu bezpečnosti použije pro každou sérii nový nástroj, který je následně vyřazen - ještě před dosažením plné produktivní životnosti. Čas obrábění je pouze jedním faktorem v celkovém kontextu. U výroby HMLV často dochází k tomu, že manipulace s různými obrobky a upínacími přípravky či výměna nástrojů a břitových destiček často trvá déle, než je vlastní doba obrábění. Zdrojem skrytých nákladů mohou být i záležitosti nástrojového vybavení, stavu a možností obráběcího stroje, prostojů, přímé práce a materiálů obrobku. Moderní přístup k ekonomice výroby náklady na nástroje a materiál obrobku, vybavení a výrobní náklady, náklady na zařízení během odstávky, mzdy a náklady na údržbu zohledňovat musí.
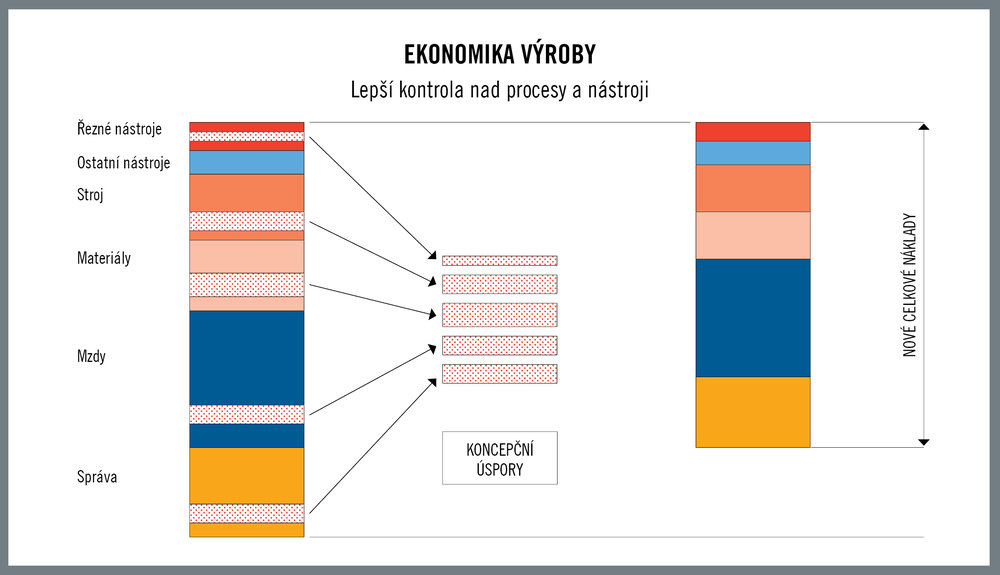
HQ_ILL_Ekonomika_vyroby
Obrázek 3
Rychle se měnící požadavky v situaci HMLV dosahování vysoké výtěžnosti značně komplikují. V případě dlouhodobých výrobních sérií HVLM mohou zkušební série s následným seřízením zajistit výnos blížící se 100 %. Na druhou stranu může být výtěžnost v situaci HMLV podvojná. Úspěšná výrobní série s jedním dílem představuje 100procentní výnos, pokud však bude díl nepřijatelný nebo zmetkový, bude výnos nulový. Požadavky na kvalitu, rentabilitu a časovou efektivitu zůstávají stejné, výnos z výroby prvního dílu se ale stává prvořadým požadavkem. V takovém případě je patrně nejdůležitějším hlediskem zabránění poškození nástroje. Jednou z výhod malých výrobních sérií je to, že se z opotřebení nástroje stává nejméně kritický faktor a výroba může v rozumné míře použít agresivnější a produktivnější řezné parametry.
Důležitý a neustále se měnící faktor představuje určení vhodného okamžiku pro výměnu nástroje. Přílišné otálení může vést k poškození nástroje a k přerušení výroby, nebo dokonce k poškození obrobku. Častá výměna nástrojů na druhou stranu zvyšuje náklady na samotný nástroj plus ztracený čas při zastavování stroje a výměně nástroje. Určení doby, kdy je třeba nástroj vyměnit, vyžaduje vyhodnocení vztahu změn vzhledem k celému obráběcímu systému, vytvoření protokolu výměny nástrojů a jeho důsledné dodržování.
Závěr
Vzájemné vazby mezi faktory procesu obrábění kovů nejsou vždy jedna ku jedné. Změna řezných podmínek, materiálu obrobku nebo objemu výrobků má dopad na životnost nástroje i další aspekty obráběcího procesu. Pro výrobní ekonomiku každého výrobního závodu je důležité si tyto vztahy uvědomit a vyvinout pragmatické strategie pro jejich řízení. Každý zaměstnanec výroby však není profesorem matematiky a nemá ani prostor tyto vztahy studovat do hloubky. Proto přicházejí dodavatelé s nabídkou procesní analýzy a služeb managementu (viz postranní panel), které poskytují výrobcům ucelený náhled na jejich konkrétní provozy a vedení pro dosažení maximální produktivity a rentability jejich úsilí.
Častým steskem výrobců je, že mají spoustu práce a platících zákazníků, ale přesto přicházejí o peníze. Řešením jejich problémů je rozpoznání skutečnosti na základě všech faktorů zapojených do současné výrobní ekonomiky a zjišťování a následná eliminace opomenutých a skrytých nákladů, které provozům v dosahování maximálního výnosu brání.
Postranní panel
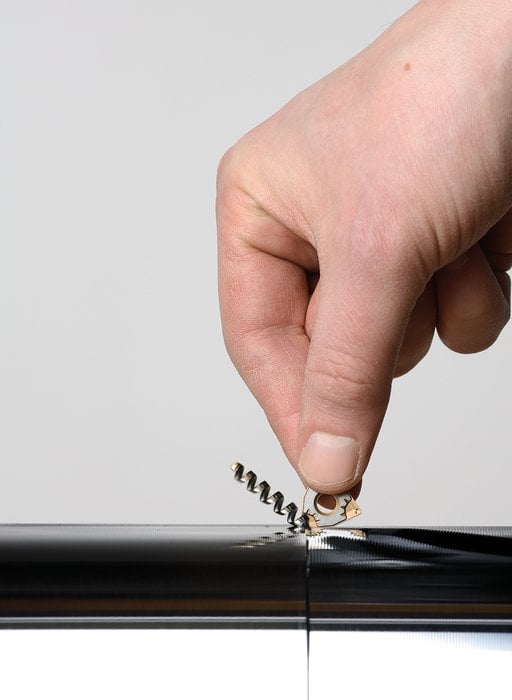
HQ_IMG_Duratomic_cip.jpg
Obrázek 4
Automatizovaná analýza
Od počátků hromadné výroby se počet faktorů ovlivňujících produktivitu výroby a náklady zmnohonásobil. Spolu se stále komplexnějšími obráběcími operacemi a vybavením jsou i vztahy mezi jednotlivými faktory výrobního procesu mnohem složitější. Žádný z prvků neexistuje sám o sobě – změna požadavků na objem výstupu například ovlivní náklady na nástrojové vybavení, zařízení, údržbu, práci a další.
Již samotné určení počtu spolupůsobících faktorů a jejich vzájemných vazeb představuje velkou výzvu. Nárůst složitosti výrobních procesů vyžaduje systematický přístup k jejich měření, sledování a řízení.
Analýza produktivity a nákladů (PCA) společnosti Seco prozkoumá celý výrobní proces a nalezne nejlepší způsoby, jak snížit náklady a zajistit zvýšení produktivity. Základem systému jsou desítkami let ověřené výrobní zkušenosti a znalosti společnosti Seco v celosvětovém měřítku. Tyto znalosti jsou aplikovány v kombinaci s důmyslnou počítačovou analýzou a algoritmy zahrnujícími například i simulační techniky Monte Carlo, které umožňují automatizaci modelování nákladů.
Kvalifikovaný zástupce společnosti Seco provede analýzu PCA, která vyhodnotí veškeré nástroje a technologie používané ve výrobním procesu a vygeneruje souhrnný protokol obsahující procesní informace, jako jsou data o obráběcích nástrojích a řezné parametry, a přehled o nákladech zahrnující náklady na díl, hodinovou výkonnost a investiční náklady. Software PCA dokáže vyhodnotit postupy od jedné obráběcí operace až po úplnou cestu obrobku ve výrobním závodě.
Zaměřuje se na aspekty dosažení vyšší produktivity, které mají největší vliv na výši vynaložených nákladů. Systém zohledňuje limitující faktory a provozní omezení a dokáže rozpoznat potřebu podrobnějších studií.
Na základě srovnávací časové a nákladové studie příslušného provozu nebo závodu software PCA v počáteční fázi analyzuje faktory nástrojového vybavení včetně procesních parametrů, cyklových časů a požadavků na výkon. Druhá fáze zahrnuje stejný proces, přičemž však optimalizuje řezné podmínky a volbu vhodných nástrojů. Třetí fáze může zahrnovat změny procesů, kombinaci operací a prozkoumání větších změn, jakou může být až modernizace obráběcích strojů.
Výrobci, kteří systém Seco PCA využívají, mohou očekávat až 30procentní úsporu celkových nákladů a zvýšení produktivity až o 40 procent, a to bez ohledu na průmyslové odvětví.
Autor:
Patrick de Vos, Corporate Technical Education Manager, Seco Tools