www.modernitovarna.com
03
'18
Written on Modified on
Globální analýza opotřebení nástroje odkrývá více než jen technologii obrábění
Řezné nástroje jsou „základním prvkem“ procesu obrábění kovů. V závislosti na tom, jakým způsobem jsou nástroje vybírány a používány, nabízejí potenciál k nárůstu produktivity obrábění, nebo naopak výkonnost výroby limitují. To je z velké části ovlivněno způsobem využití řezného nástroje v rámci celého výrobního procesu.
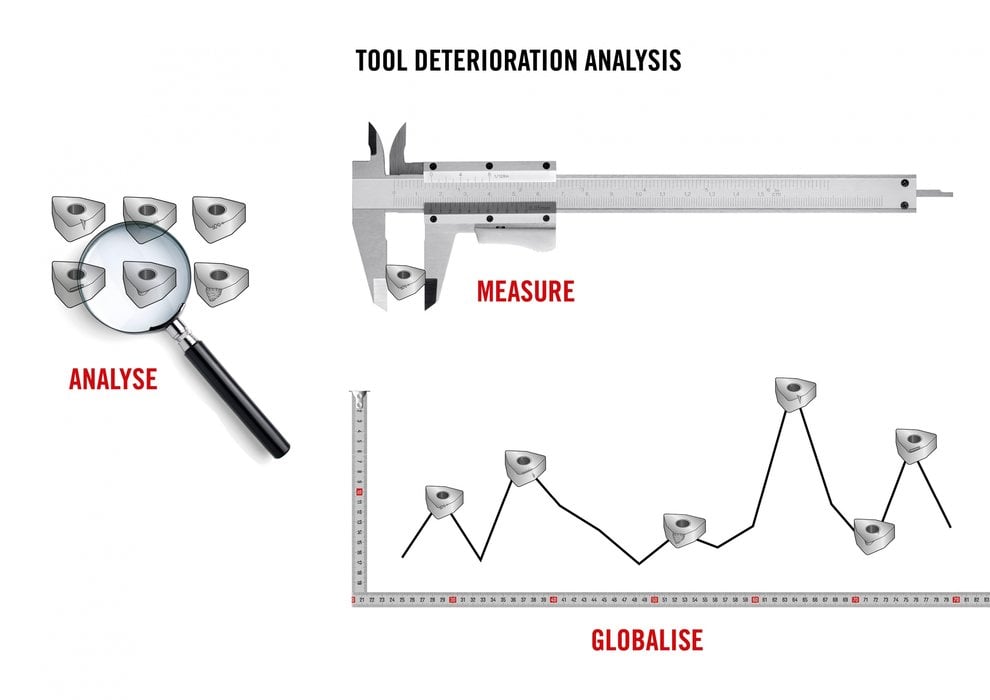
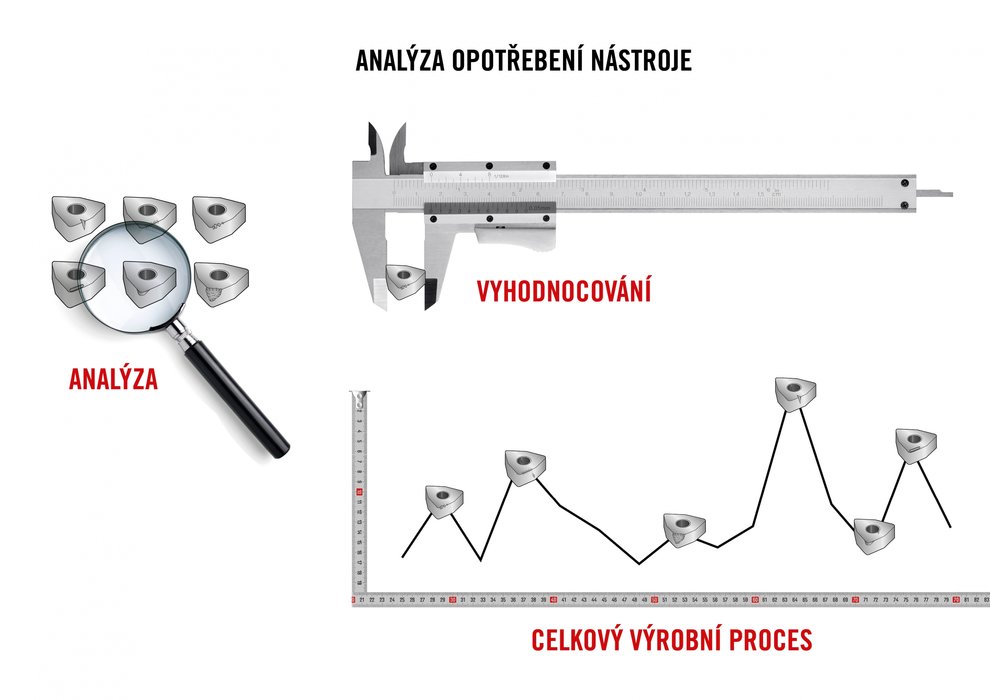
Obrázek 1
Obráběcí nástroje jsou ze své podstaty spotřebním materiálem; dochází k jejich opotřebování, až nástroj přestane obrábět efektivně a dojde ke ztrátě jeho funkčnosti. Tradiční přístup ke správě nástrojů využívá samostatnou analýzu opotřebení, která se zaměřuje na práci s řeznými materiály, geometriemi a řeznými podmínkami pro danou aplikaci s cílem zvýšit množství obrobených dílů a životnost nástroje při vybrané operaci. Chceme-li však maximalizovat efektivitu celého výrobního procesu, je třeba kromě opotřebení nástroje zvážit také mnoho dalších faktorů. Je nezbytné hlouběji analyzovat zhoršení kvality řezného nástroje v kontextu celkového („globálního“) výrobního procesu.
Globální analýza opotřebení nástroje (GTDA) přesahuje rámec základního hodnocení opotřebení nástroje a zahrnuje skutečnosti související s nástrojovými systémy, jako je např. čas potřebný na manipulaci s nástroji, záležitosti nevztahující se přímo k opotřebení, ekonomika výroby, organizace výroby, přístup a předpoklady pracovníků, správa datových toků a celkové výrobní náklady. Analýza GTDA je založena na pravidelném vyhodnocování velkého počtu nástrojů použitých ve výrobě, které jsou náhodně vybírány k sestavení komplexního přehledu o jejich přínosu k celkové efektivitě výrobního procesu.
Globální výrobní proces
Studie opotřebení nástroje se obvykle omezuje na jediný nástroj použitý v konkrétní obráběcí operaci. Kvůli průkaznosti výsledků je však nezbytné prověřit opotřebení (degradaci) nástroje
v souvislosti s veškerým nástrojovým vybavením používaným ve výrobních procesech podniku. Výrobní proces (Obrázek 2) začíná získáváním surovin či polotovarů a plánováním, což zahrnuje využití lidského intelektu, technologických zdrojů a kapitálových investic. Tento proces pokračuje aktivitami zvyšujícími přidanou hodnotu a umožňujícími vznik přidané hodnoty, zároveň ale může být limitován činnostmi, které vedou ke ztrátě prostředků, času a intelektuálních zdrojů a v důsledku snižují kvalitu dílů a zisk z výroby. Výstup se vyhodnocuje s ohledem na kvalitu dílů, potřebné množství, požadovanou dobu výroby a výši vynaložených nákladů.
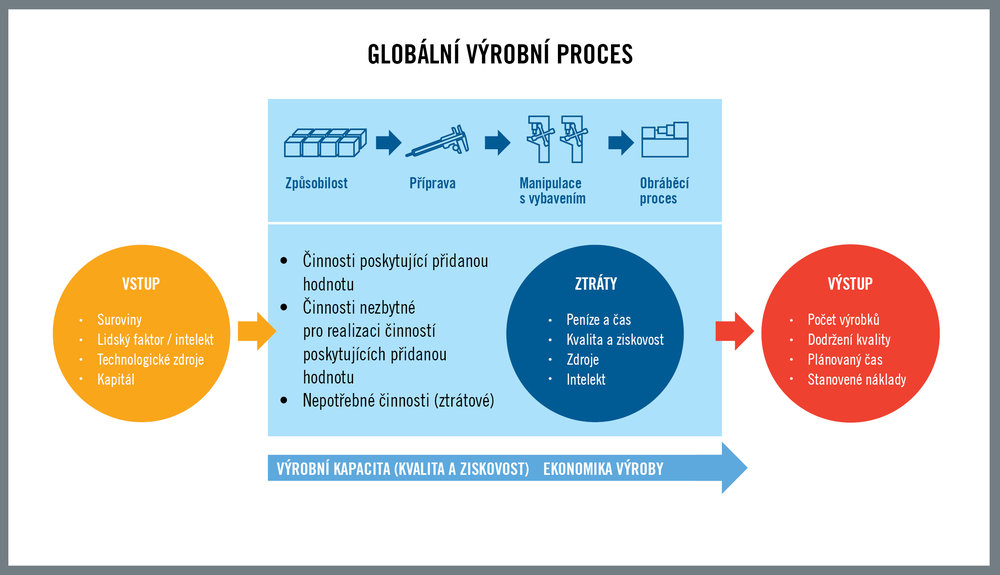
HQ_ILL_Global_Manufacturing_Process.jpg
Obrázek 2
Evoluce výrobního procesu
Metody používané k analýze a předvídání životnosti nástroje závisí na způsobu použití nástrojů. Po staletí se výrobní postupy vyvíjely od ručního zhotovování individuálních výrobků po hromadnou výrobu standardizovaných dílů. Zdokonalování výrobních postupů pak přineslo druhou generaci hromadné výroby, která je schopna produkovat stále větší objemy podobných dílů – výroba s velkým objemem a nízkou variabilitou výrobků (HVLM). V poslední době digitální technologie aplikovaná v řízení programovatelných obráběcích strojů a systémech pro manipulaci s obrobky pomohla realizovat třetí generaci hromadné výroby umožňující nákladově efektivní vysoce různorodou výrobu malých objemů (HMLV).
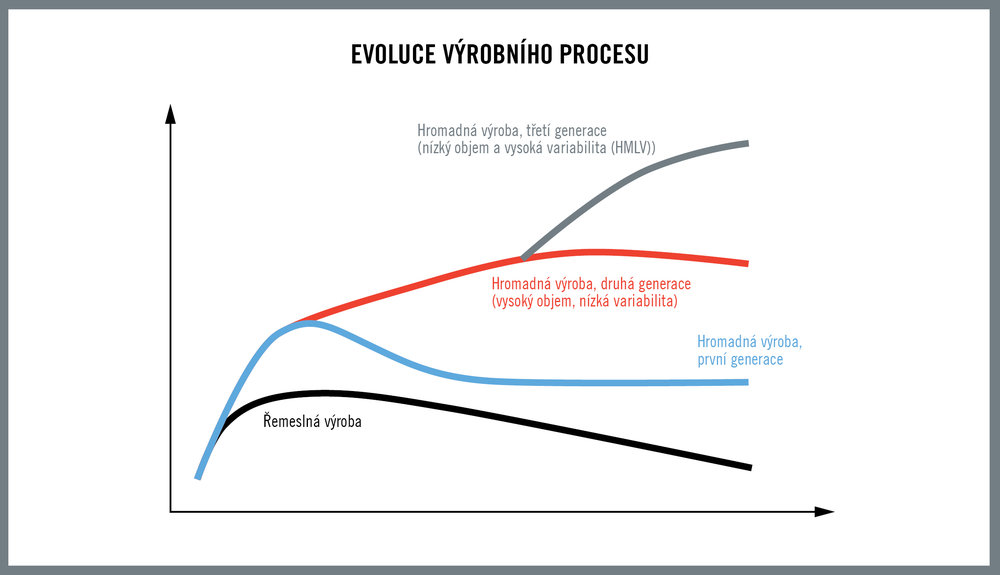
HQ_ILL_Manufacturing_Process_Evolution.jpg
Obrázek 3
Ačkoli klíčové problémy s výkonností výroby zůstávají stejné – zejména dosažení nákladové a časové efektivity, určité minimální kvality a určité úrovně zisku – vyžadují postupy druhé a třetí generace hromadné výroby odlišné přístupy k analýze životnosti nástroje. Při výrobě typu HVLM druhé generace se shodné díly vyrábějí ze stejného materiálu ve výrobních sériích trvajících několik dní, měsíců nebo let s použitím stejného vybavení a stejného druhu obráběcích nástrojů. V této situaci je řízení životnosti nástroje relativně jednoduché. Pracovníci výroby použijí prototypy a zkušební série k určení nejlepší průměrné životnosti nástroje. Následně se vydělí požadovaný objem dílů očekávanou životností jednotlivých nástrojů.
Konzistentní data očekávané životnosti nástroje umožní výrobnímu závodu naplánovat výměny nástrojů, které maximalizují využití nástroje a podporují nepřetržitou výrobu. Výrobní postupy HVLM však v současné době přestávají být v popředí zájmu. Kvůli vyvážení skladových zásob a poptávky a také z důvodu zakomponování probíhajících konstrukčních změn výrobci stále častěji upouštějí od produkce dílů v dlouhých neměnných výrobních sériích.
Současně se začíná více prosazovat třetí generace výrobních strategií hromadné výroby HMLV. Rychle přizpůsobitelné procesy HMLV se dobře adaptují na současné skladovací a konstrukční cíle, proces plánování se tím ale stává mnohem složitějším. Po sérii deseti kusů může následovat série dvou, pěti nebo pouze jednoho dílu. Materiály obrobku se mohou změnit
z ocele na hliník a následně na titan a geometrie dílů z jednoduchých na složité. Na určení životnosti nástroje pomocí zkušebních sérií není k dispozici dostatek času.
V takových případech výroba obvykle udělá konzervativní odhad plánované životnosti nástroje a z důvodů bezpečnosti použije nový nástroj pro každou sérii a následně nástroj vyřadí – ještě před koncem jeho skutečné produktivní životnosti. Globálnější přístup k analýze opotřebení nástroje může pomoci minimalizovat nedostatečné využití kapacity řezného nástroje.
Potenciální výnosy
Rychle se měnící výrobní postupy HMLV komplikují dosahování vysokoprocentní efektivity výtěžnosti obráběcích operací. V případě dlouhodobých sérií HVLM mohou zkušební série
s následným seřízením zajistit výnos blížící se 100 %. Na druhou stranu může být výtěžnost v situaci HMLV podvojná. Úspěšná výrobní série s jedním dílem představuje 100procentní výnos, ale když bude díl nepřijatelný nebo zmetkový, bude výnos nulový.
Požadavky na kvalitu, rentabilitu a časovou efektivitu zůstávají stejné, výnos z výroby prvního dílu se ale stává prvořadým požadavkem. V takovém případě je patrně nejdůležitějším hlediskem zabránění poškození nástroje. Jednou z výhod krátkých výrobních sérií je to, že se
z opotřebení nástroje stává nejméně kritický faktor a výroba může v rozumné míře použít agresivnější a produktivnější řezné parametry.
Zručnost a lidský faktor
Zdlouhavé a neměnné výrobní série HVLM minimalizují vliv lidského faktoru na výrobní proces. Po zahájení dlouhodobé série je možné operace v podstatě automatizovat. Dokonce
i v případech, kdy se obsluha účastní každé výměny dílů, stále se opakující povaha těchto operací minimalizuje vliv obsluhy a programátorů. Flexibilita není nutná, může být spíše na škodu.
Na druhou stranu rychle se měnící scénáře HMLV kladou opět důraz na zapojení člověka do procesu, a to do té míry, že úkony vyžadují určitou míru tradiční řemeslné zručnosti zahrnující kreativitu a flexibilitu efektivně se adaptovat na neustále se měnící díly a řezné podmínky, což jsou charakteristické rysy obrábění typu HMLV.
Zaměření na postup namísto výsledků
Mnoho snah o výrobní procesní analýzu se zaměřuje na vyhodnocení konečného výsledku vzhledem k životnosti nástroje a množství vyrobených dílů bez důkladnějšího přezkoumání samotného procesu. Může dojít k opomenutí problémů souvisejících s řeznými nástroji, které přímo nesouvisí s životností nástroje, avšak jsou limitujícím faktorem výroby. Například otřepy se životností nástroje obvykle nesouvisejí, avšak jejich výskyt výrobní proces narušuje, neboť je nutné připravit a implementovat další operaci na jejich odstranění.
Tvorba otřepů však souvisí s geometrií nástroje a parametry aplikace, a proto musí být zohledněna v analýze opotřebení nástroje. Poškození nástroje, což je další problém, který obvykle přímo nesouvisí s jeho opotřebením, ovšem souvislost s materiálem a geometrií nástroje, parametry aplikace a obráběcími faktory má.
Prvky provozní dokonalosti
Základním prvkem pro zajištění efektivity výroby je eliminace plýtvání, nepružnosti a různorodosti. Komplexní analýza opotřebení nástroje zohledňuje pět prvků provozní dokonalosti.
Nejprve je nutné důkladně porozumět celému obráběcímu procesu a vztahu mezi obráběcí operací a materiálem obrobku. Za druhé je potřeba věnovat pozornost redukci ztrát prostřednictvím strategií štíhlé výroby a dalších iniciativ. Za třetí je potřeba aplikovat koncepty ekonomiky výroby a zajistit její ziskovost. Za čtvrté je potřeba zvážit procentuální cíle výtěžnosti v kontextu objemu výroby a variability dílů. Dosažení co nejvyšší flexibility je potřeba vnímat jako způsob minimalizace limitujících faktorů. Současně je ale nutné kontrolovat variabilitu, aby byly zajištěny konzistentní tolerance dílů. Nakonec je třeba zdůraznit význam pracovníků výroby, aby bylo možné plně využít jedinečný a nenahraditelný zdroj, který představují.
Faktory přesahující opotřebení nástroje
Globální analýza nástrojů doplňuje počáteční měření opotřebení hran břitové destičky o analýzu funkce nástroje v celkových součtech nákladů na prodané zboží (COGS), analýzy Single-Minute Exchange of Die (SMED), výsledků řízení toku hodnot (VSM) a celkové efektivity vybavení (OEE) v procentech.
Nejzákladnější ekonomické hledisko související s nástroji je jasné: nástroje stojí peníze. Obrázek 4 představuje náklady na různé prvky obráběcího procesu a jejich celkový souhrn jako hodnotu COGS. Tyto údaje umožňují výrobě vzájemně porovnávat různé složky výrobních nákladů
s cílem odhalit možnosti snižování nákladů, které mohou zvýšit ziskovost provozu.
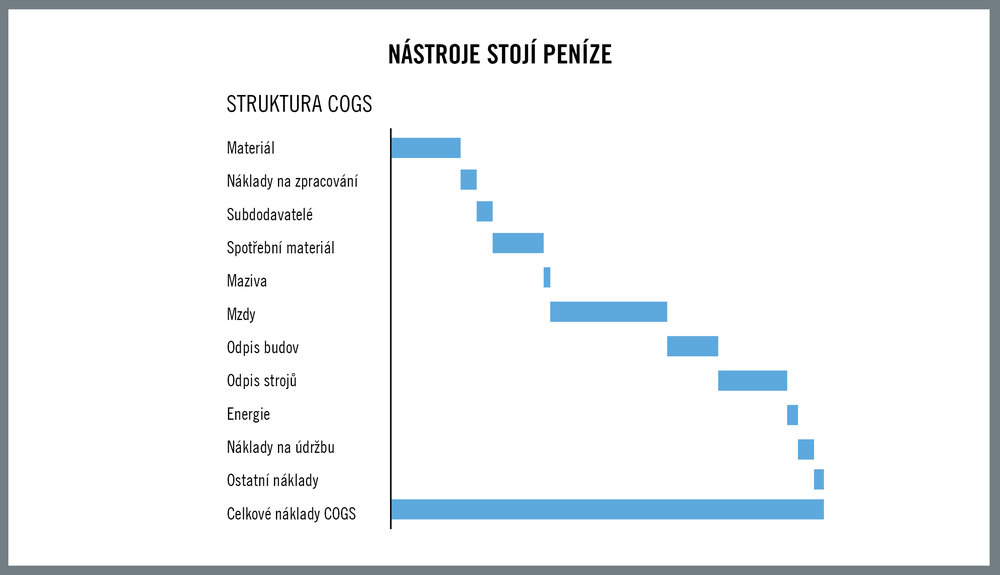
HQ_ILL_Tools_Cost_Money.jpg
Obrázek 4
Další ekonomický faktor související s nástroji je doba potřebná na manipulaci s nástroji mimo vlastní obráběcí provoz. Čas vynaložený na výměnu a přípravu nástrojů je vyhodnocován analytickými postupy SMED, které rovněž poskytují náhled na náklady nad rámec pouhých nákladů generovaných v souvislosti s opotřebením a výměnou nástroje. Část těchto nákladů vzniká při pořizování a organizaci nástrojů, jejich upínání a nahrávání programů do obráběcího stroje.
Hodnota OEE určuje, do jaké míry je efektivně využívána dostupná výrobní doba. Analýza OEE detekuje ztráty, provede posouzení pokroku a napomáhá zvyšování produktivity prostřednictvím eliminace neefektivit. Tato analýza identifikuje celkový čas dostupný pro výrobu, následně odečte plánované odstávky, neplánované prostoje, výměny, kratší výpadky a snížení rychlosti, odpad a přepracování a poskytne efektivní dobu obrábění vyjádřenou
v procentech celkové dostupné doby. 100 procent OEE je úctyhodný, v praxi nedosažitelný cíl, kdy je díl vyráběn v určené kvalitě, co nejrychleji a bez jakýchkoli časových ztrát.
Analýza VSM ilustruje potřebu rovnováhy mezi zlepšováním výkonu jednotlivých článků výrobního procesu. Obrázek 5 představuje grafické znázornění vlivu zlepšení výkonnosti jednoho elementu systému bez zlepšení ostatních. Představte si veslaře na lodi. Vyšší výkon jednoho veslaře je ke škodě výkonnosti celé lodi.
Vylepšení částí procesu je nutné provádět s přihlédnutím k jejich vztahu k objemu a rozmanitosti výroby, charakteristikám materiálu obrobku, geometrii dílů, požadavkům na obráběcí stroje a upnutí a dalším faktorům za účelem dosažení a udržení celkově vyvážených výrobních operací.
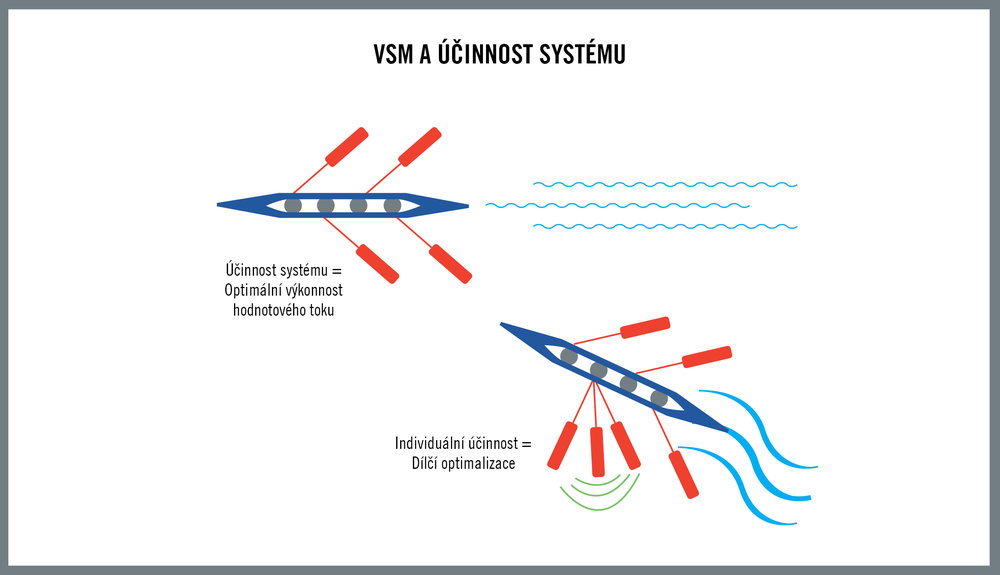
HQ_ILL_VSM_And_System_Efficiency.jpg
Obrázek 5
Globální analýza opotřebení nástroje
Analýza GTDA je v podstatě jednoduchý proces. Postupně jsou zkoumány řezné hrany velkého počtu náhodně zvolených nástrojů z celé výroby a určuje se, které břity jsou opotřebované. Opotřebení se klasifikuje podle typu a jeho míry. Zatímco se tradiční analýza opotřebení nástroje soustředí na jeden nástroj v rámci jedné operace, GTDA shromažďuje informace o opotřebení nástroje a další informace týkající se nástrojů z celé výroby. Následně aplikuje analýzy COGS, SMED, VSM, OEE a další analytické nástroje a sestaví doplňková data, která poslouží jako vodítko pro plánování a implementaci zlepšovacích programů.
Úspěch závisí na tom, zda bude mít výrobní provoz potřebnou disciplínu k realizaci programu GTDA. Stejně tak je důležité pokračovat v pravidelných analýzách nástrojů a dat. Rovněž je vyžadována další forma disciplíny – poctivý přístup. Výroba musí pravdivě a objektivně přijímat výsledky analýz a mít ochotu na základě jejich zjištění podniknout navržené kroky bez ohledu na tradice a zásady provozu nebo nepodporované názory ohledně parametrů použití nástrojů.
Závěr
Opotřebení nástroje je nevyhnutelné a řízení tohoto jevu je nezbytné k zajištění úspěšných obráběcích operací. Opotřebení nástroje však představuje pouze jeden z množství vlivů řezných nástrojů na efektivitu celkového výrobního procesu. GTDA jde dál než analýza opotřebení jednotlivých nástrojů, neboť zahrnuje všechny nástroje ve výrobě a současně zohledňuje i širokou řadu významných vlivů souvisejících s nástroji mimo proces obrábění.
Postranní panel:
GTDA: Proč a jak
Během vrcholného období velkoobjemové hromadné výroby jednotlivých dílů se jednoduše měřilo, upravovalo a vyvažovalo opotřebení nástroje tak, aby se maximalizovala jeho životnost a množství obrobených dílů. S tím, jak se výrobní strategie vyvinuly do podoby více variabilní a just-in-time výroby téměř zakázkových součástí, stalo se samotné opotřebení nástroje
v celkovém výrobním procesu okrajovější záležitostí.
Tým pro konzultantské služby společnosti Seco průběžně analyzuje probíhající výrobní evoluci a jeho odpověď na neustálé změny ve výrobním průmyslu představuje vlastní výrobní model „NEXT STEP“ (DALŠÍ KROK) (Obrázek 6). Model NEXT STEP je založen na čtyřech klíčových standardech obrábění, kterými jsou rentabilita, časová efektivita, kvalita a zisk. Model Next Step umožňuje výrobcům nastavit a plnit vlastní normy pro obrábění prostřednictvím analýzy ztrát ve výrobě, technologie obráběcího procesu, vědy o materiálech nástrojů a obrobků, ekonomiky výroby a výtěžnosti a kritické role zaměstnanců a vedení v příslušných operacích.
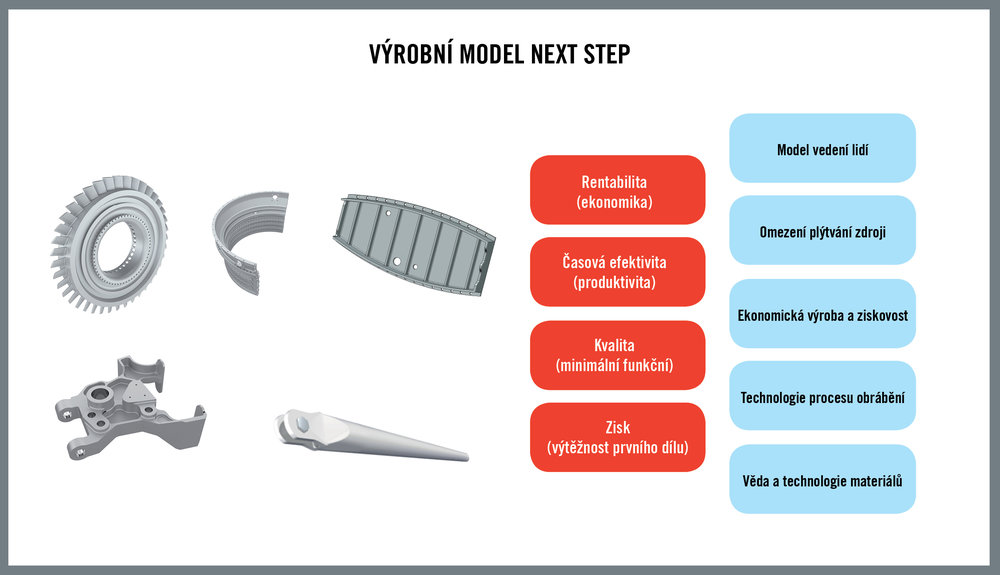
HQ_ILL_Next_Step_Production_Model.jpg
Obrázek 6
Globální analýza opotřebení nástroje (Obrázek 7) je klíčovou složkou vyhodnocování a vylepšování výrobního procesu jako celku. Prostřednictvím přezkoumání náhodně zvoleného výběru nástrojů, který pokrývá všechny oblasti obrábění ve výrobním procesu, a následného využití množství naměřených hodnot z výroby získá výrobce širší porozumění o funkci, kterou zastávají nástroje v celém procesu obrábění. GTDA pomáhá výrobcům zjistit možnosti pro zvýšení výkonu nástrojů a produktivity a současně identifikovat skutečnosti, které mohou působit časové a finanční ztráty ve výrobě.
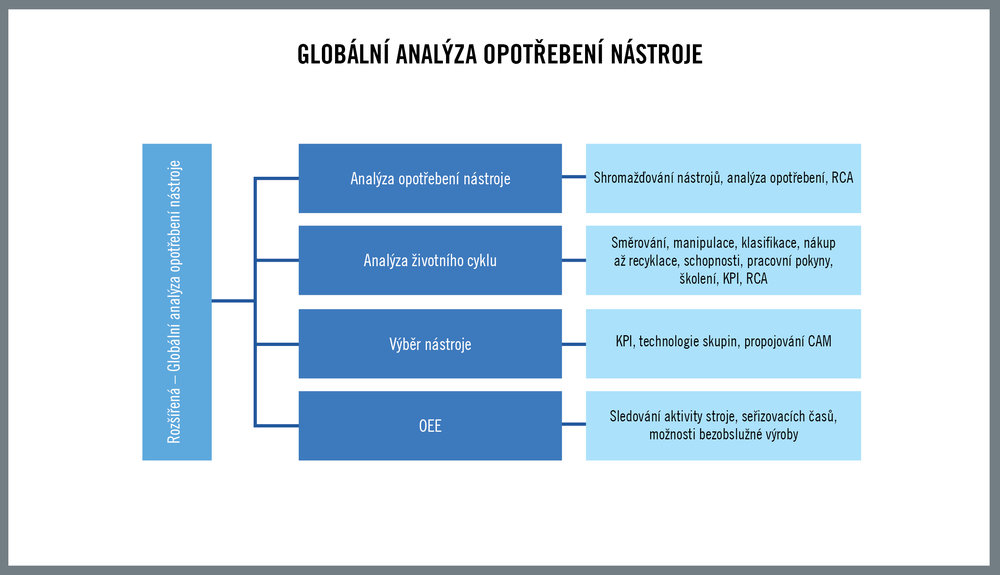
HQ_ILL_Global_Tool_Deterioration_Analysis.jpg
Obrázek 7
K tématu GTDA vydala divize Konzultantských služeb Seco publikaci s názvem „Tool Deterioration: Best Practices (Opotřebení nástroje: Osvědčené postupy)“ (Obrázek 8). Tato publikace prezentuje opotřebení nástroje jako bod rovnováhy pro modely obrobitelnosti, přičemž upozorňuje, že většinu problémů v procesech obrábění lze klasifikovat jako události související s opotřebením nástroje. Příručka pojednává o různých aplikacích při obrábění kovů a je určena k tomu, aby poskytla náhled do problematiky příčin opotřebení nástroje, zatímco současně nabízí přehled „osvědčených postupů“, jak identifikovat, řešit a mít pod kontrolou procesy opotřebení nástrojů.
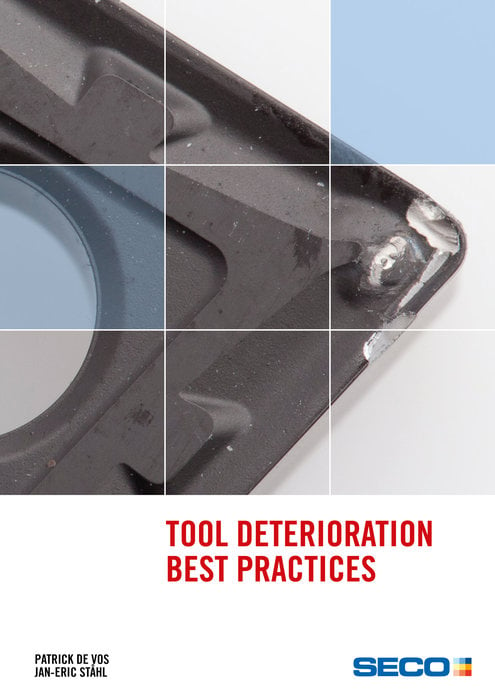
HQ_IMG_Tool_Deterioration_Best_Practices_2014.jpg
Obrázek 8
Autor:
Patrick de Vos, Corporate Technical Education Manager, Seco Tools